POLYETHYLENE RAW MATERIAL
Advances in technology have also led to significant developments in the production of raw materials required for plastic pipe production. Developed in the 1950s, PE 32 class low density polyethylene plastic pipes were used in drinking water lines for the first time. Later, PE 63 raw material was developed and its use was successfully applied in systems that do not require high pressure. However, PE 63 has been used in lines requiring pressure up to 4 bars due to the technical properties of the material. Developments in raw materials continued and the second generation PE 80 raw material was introduced. Thus, PE 80 raw material began to be used with high performance in drinking water and natural gas networks. The 3rd generation PE 100 pipe raw material, developed in the early 1990s, has become both a high performance and economical solution for use in drinking, potable water and natural gas networks.
- 1. Generation Materials : PE 32 (LDPE), PE 40 (LDPE),PE 63 (HDPE)
- 2. Generation Materials : PE 80 (MDPE),PE 80 (HDPE)
- 3. Generation Materials : PE 100 (HDPE)
Polyethylene 100 is the strongest and highest pressure resistant PE pipe material known today. It has a longer wall thickness and therefore a larger inner diameter than PE 40 and PE 80 pipes at the same operating pressure and diameter. Thus, one size smaller pipe can be used for the same flow rate.
As the density of PE materials increases, mechanical strength values also increase. When a pipe with the same working pressure is produced from different raw materials, the decrease in wall thickness is seen in the figure below. If a pipe with an outer diameter of 110 mm and a working pressure of 10 bar is produced from PE 32, PE 63, PE 80 and PE 100 raw materials, its wall thicknesses and weights will be as given below.
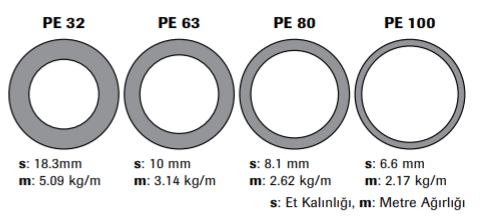
The color of SANBOR PE 100 pipes is blue and black. SANBOR PE pipes are produced in coils up to Ø 125 mm, and in lengths of 12-13 m for diameters of Ø 125 mm and above. SANBOR produces PE 100 pipes with these features according to the TS EN 12201-2+A1 standard with the assurance of ISO 9001
ADVANTAGES OF SANBOR PE 100 POLYETHYLENE PIPES
- PE 100 Polyethylene Pipes have high flexibility. In this way, they provide ease of assembly. Elongation at break is minimum 350%.
- PE 100 Pipes are not affected by underground movements and have no breaking properties.
- PE 100 Pipes have high impact resistance and crack propagation resistance.
- Since PE 100 Pipes have low internal surface roughness, they provide significant advantages when choosing diameters during project design.
- PE 100 Pipes are suitable for laying underwater and are not affected by sea water and sea movements.
- There is no assembly loss due to the joining methods of PE 100 Pipes.
- PE 100 Pipes operate smoothly at nominal operating pressure for at least 50 years.
- PE 100 Pipes are resistant to UV rays.
- PE 100 Pipes are not affected by harmful substances in the soil structure that cause corrosion. Therefore, there is no need for cathodic protection.
- PE 100 Pipes are resistant to chemicals.
- PE 100 Pipes do not change the smell and taste of water, therefore they are healthy.
- It is not possible for plant and tree roots to enter polyethylene pipes.
- PE 100 Pipes can be produced optionally in any pressure class from PN 4 to PN 25.
- PE 100 Pipes can be produced in coils and lengths.
- Due to the excellent welding properties of PE 100 Pipes, they do not come out of the joints or break under pressure, and they provide sealing.
USAGE AREAS OF SANBOR PE 100 PIPES
- In underground and aboveground drinking and potable water networks
- Agricultural irrigation systems
- Marine discharge systems
- Wastewater and solid waste discharge systems
- Fire water and cooling systems
- Submarine transit lines
- Pharmaceutical and chemical industry
- petrochemical industry
- Food industry
- In maritime and fishing
- It is used in telecommunication cabling systems and many areas.
WALL THICKNESS AND WEIGHT TABLE OF SANBOR PE 100 PIPES ACCORDING TO PRESSURE
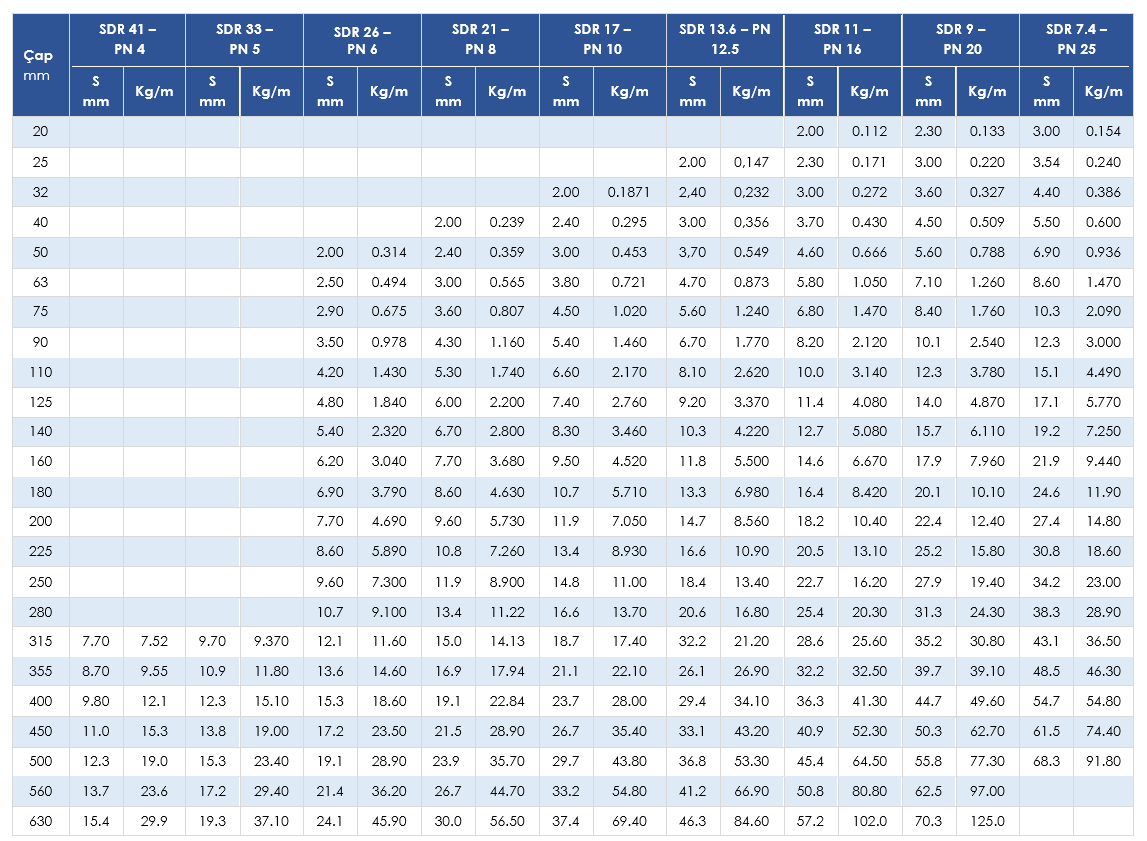
USAGE AREAS OF POLYETHYLEN PIPES
Usage Areas |
PE 40 LDPE |
PE 63 LDPE |
PE 80 MDPE |
PE 100 HDPE |
Drinking water pipelines
|
|
*
|
*
|
* |
Pressurized irrigation pipelines
|
|
* |
*
|
* |
Main Line connection applications
|
* |
*
|
*
|
* |
hydroelectric power plants
|
|
|
|
* |
Gas Lines
|
|
|
*
|
* |
Treatment plant pipeline
|
|
|
*
|
* |
Drinking water treatment installation
|
|
|
*
|
* |
Swimming pool pipeline
|
|
|
*
|
* |
Cooling water pipeline |
|
|
* |
* |
Compressed Air Lines |
* |
|
* |
* |
Solids transport lines |
|
|
* |
* |
Pipeline for chemicals |
|
|
* |
* |
Sheathed geothermal heating pipes |
|
|
* |
* |
Cable Protection Pipes |
|
|
* |
|
Sewer pipelines |
|
|
* |
|
Solid waste methane gas discharge |
|
|
* |
* |
Solid waste drainage line |
|
|
* |
|
Sea discharge application |
|
|
* |
* |
Fish farm application |
|
|
* |
|